This article covers an advanced method for reducing the amount of material used during the manufacture of 3D printed parts, as well as the parameters that must be followed to ensure a successful print. Specifically, we will discuss how to minimize the amount of material used for both supports and infill by using the parameter gradual steps.
In the world of 3D printing, FFF (Fused Filament Fabrication) is the process of melting previously coiled thermoplastics and depositing them on a platform to produce a succession of layers that, once completed, form our object in three dimensions.
As a result of this type of additive manufacturing technology, parts can be created that are essentially empty, allowing us to use less material while still achieving our goals.
To ensure the strength of the part, mesh patterns are generated inside the part; the denser the mesh is, the stronger the part. Despite this, this process will take more time since more material needs to be deposited. This process of internal meshing is known as filling.
A major disadvantage of FFF technology is the need for support at a certain cantilever angle, which will primarily be determined by the material, nozzle, and layer height used. Using the same mesh patterns as the fill material will enable the necessary sections of the part to be generated correctly. We can therefore conclude that designs without supports are in fact more sustainable since the support material is a residue of the printing process rather than a necessary component.
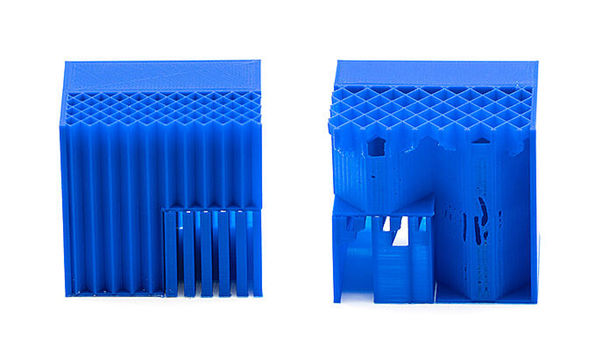
The infill material that we use inside the part does not only provide strength to the 3D printed object, but supports the upper portions of the object, which are also known as ceilings or upper faces.
It is common for 3D printed parts to require a substantial amount of support and filler material. Although we would like to reduce the amount of material consumed, we cannot reduce the density of these two parameters too much. This is because the part will be put at risk. For example, the supports may leave a poor finish, or there may not be sufficient filler, which would result in the ceilings or upper walls not being deposited correctly. Essentially, while reducing the density of the supports and infill will make the 3D printing process faster and require less material, if the piece does not turn out well, all the material will be wasted, making the saving ineffective.

We can find a lot of waste material in large pieces, and if the 3D printed part requires support in the last layers, support towers will generate a lot of waste material. It is possible to use the minimum amount of material by activating the gradual steps command, which can be located in both the fill and support parameters. As a result of this parameter, the density will vary according to how close our part is to the support.
In the case of the infill, it will begin with a wider mesh, which will become increasingly denser as it approaches the upper layers.

Supports will be handled in the same manner; they will begin with a wide mesh and, as they approach the lower faces, they will generate increasingly dense patterns so that these lower faces, and therefore the supports, will be properly supported.
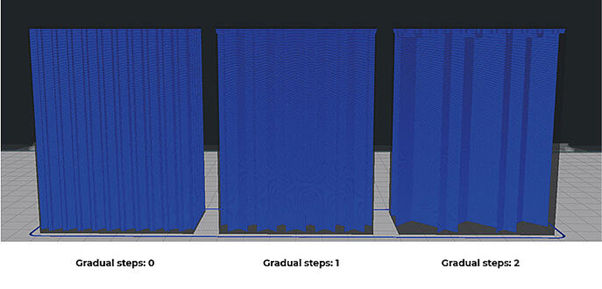
On the top bar, you can access configure settings visibility if this command is not displayed.
There are two commands to be activated: gradual infill steps and gradual infill step height for the fill, and gradual support infill steps and gradual support infill step height for the supports.
Normally, we will find the gradual infill steps and gradual support infill steps commands set to 0. Infill density is halved as it moves away from the upper surfaces by this parameter. Until the infill or support density is reached, the areas closer to the upper surfaces have a higher density. The higher the number, the more material will be saved.

As a result of the gradual infill step height and the gradual support infill step height, the height of the fill of a certain density before changing to half density can be determined. In essence, it is the distance between one density and half density. By default, this value is set to 1mm. As this value increases, the machine will be able to deposit material more accurately.
By using this parameter properly, you will be able to minimize your material waste, as well as save time during the printing process.
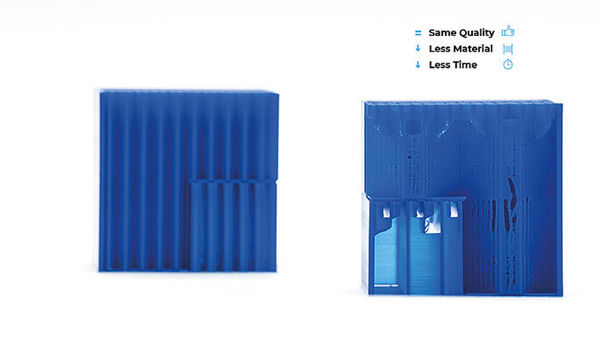
If you would like to know more in details, you may contact Eye-2-Eye.
We are here to help you!
Eye-2-Eye Communications is committed to providing innovative solutions that help our customers grow their business and be more competitive!
Click Here to find out more about the 3D printers we use and represent.
Comentarios