Tre Zeta Group, a footwear manufacturer based in Tuscany, uses 3D printing to produce jigs for its carding process to manufacture soles for classic shoes and sneakers. The team selected the BCN3D Epsilon W50 3D printer due to its advantaged IDEX technology and the material Tough PLA due to its top-tier mechanical properties...

Comfort and style will always be of the utmost importance when it comes to footwear. Designers must be creative, innovative, and keep up to date on the latest trends - including additive manufacturing technologies - if they wish to improve these aspects and expand upon what has been done before. With the acquisition of a BCN3D Epsilon W50 3D printer, our partner CREA3D has seen first-hand how Tre Zeta Group is reducing its 3D printing time while improving its cost-effectiveness and efficiency.
Tre Zeta Group was established in 1967 in Tuscany, Italy, initially offering classic shoes, and has since expanded into sneakers. The company believes that sustainability has always been one of its main pillars. The company opened a new plant in 2021 in order to further its development of shoes.
As an organization, we are committed to innovation in all aspects of our business. This includes the development of our products and services, but also finding solutions to problems within our internal operations.
“Innovation has always been one of our prerogatives, and this has led us to learn about new technologies such as 3D printing.” – Jacopo Genre, Marketing and Sales Manager.
Stepping into Tre Zeta Group’s shoes
Tre Zeta Group manufactures soles made from polyurethane; since this material tends to oxidize, it must be oxidized by a process called carding. The process usually involves the use of traditional machines and skilled labour.
By using the BCN3D Epsilon W50 3D printer, polyurethane soles can be manufactured in a more efficient manner. The use of 3D printed centering jigs eliminates the need to perform so much manual work. After being put into CNC machines, an end-use sole is born, while avoiding any impurities or imperfections along the way.
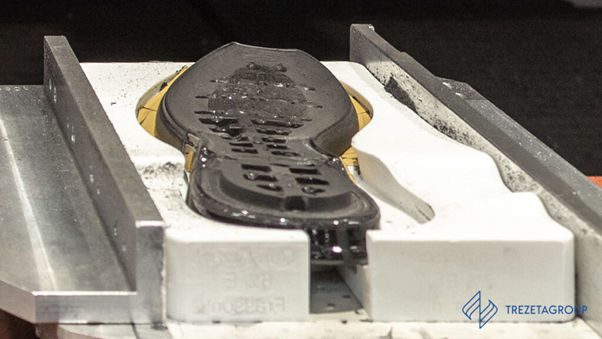
In their 3D printing process, Tre Zeta Group chooses Tough PLA as their material of choice. The fact that it is generated from waste from other processes not only provides better mechanical properties than regular PLA, but also allows the company to meet its prerogative to recycle whenever possible.
By switching to 3D printing, more consistency and shorter processing times have been achieved. Furthermore, IDEX technology has resulted in a 50% reduction in printing time.
“This has brought improvements in several aspects: a consistent product and well-defined processing times, without the need for skilled labor.” – Gianfranco Cipriano, CAD/CAM Manager.
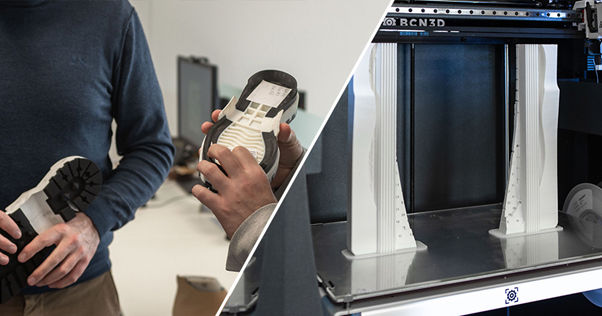
Tre Zeta Group has clearly explored multiple technologies and found that 3D printing is extremely beneficial to its overall production processes. As a result of IDEX technology, parts can be manufactured at a high speed without compromising quality, and 3D printing has once again demonstrated its potential for the future of sustainable manufacturing.
If you would like to know more in details, you may contact Eye-2-Eye.
We are here to help you!
Eye-2-Eye Communications is committed to providing innovative solutions that help our customers grow their business and be more competitive!
Click Here to find out more about the 3D printers we use and represent.
Comments